News
ISRO makes significant progress in semicryogenic engine development for launch vehicles.
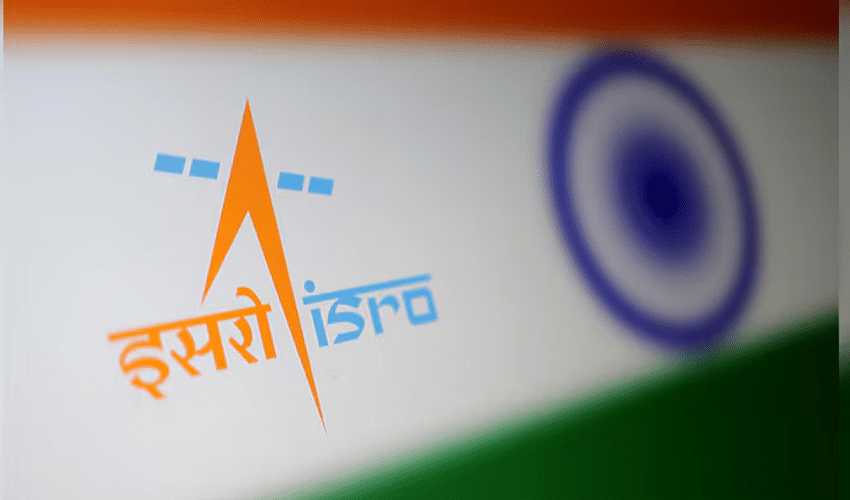
ISRO has reported significant advancements in the design and development of a Semicryogenic engine, also known as the Liquid Oxygen/Kerosene engine, with a high thrust of 2,000 kN. This engine will be used to power the Semicryogenic booster stage of the Launch Vehicle Mark-3 (LVM3). A major milestone in this development was achieved on March 28, when the first successful hot test of the Engine Power Head Test Article (PHTA) was conducted at the ISRO Propulsion Complex in Mahendragiri, Tamil Nadu. The space agency stated that the test successfully demonstrated smooth ignition and bootstrap mode operation for a duration of 2.5 seconds. The primary objective was to validate the integrated performance of key subsystems, including the pre-burner, turbo pumps, start system, and control components, through a short-duration hot firing.
ISRO confirmed that the test proceeded as expected, with all engine parameters performing as predicted. Following this breakthrough, ISRO plans to conduct a series of further tests on the PHTA to refine and validate performance before the fully integrated engine is realized. The development of the Semicryogenic propulsion engine and stage is being carried out by the Liquid Propulsion Systems Centre (LPSC) of ISRO. The new stage (SC120), powered by the SE2000 engine with 2,000 kN thrust, will replace the current core liquid stage (L110) in LVM3, enhancing payload capacity and powering future launch vehicle booster stages.
Unlike the existing propulsion system, the Semicryogenic propulsion system uses non-toxic and non-hazardous propellants—Liquid Oxygen and Kerosene—offering improved performance. The incorporation of this system, alongside an upgraded cryogenic stage in LVM3, will increase its payload capacity from 4 tonnes to 5 tonnes in Geosynchronous Transfer Orbit (GTO).
The SE-2000 engine comprises several critical subsystems, including the thrust chamber, pre-burner, turbo pump system, control components, and start-up system. Given the extreme temperatures and oxidizer-rich combustion environment, the engine requires special materials, which have been developed in collaboration with the Indian industry. The technology behind such high-thrust semicryogenic engines is highly complex and possessed by only a few nations worldwide.
ISRO also highlighted the challenges in developing the test facility for qualifying the engine and stage. The Semicryogenic Integrated Engine Test facility (SIET) was established at the Propulsion Research Complex (IPRC) in Mahendragiri for this purpose and was inaugurated by Prime Minister Narendra Modi on February 27 last year. Before integrated hot tests on the full engine, ISRO is conducting performance evaluations on an intermediate configuration called the Power Head Test Article (PHTA). This configuration includes all engine systems except the thrust chamber. The hot test conducted on Friday was the first in a planned series to validate the design of critical components, such as the propellant feed system, low-pressure and high-pressure turbo-pumps, pre-burner, start system, and control components.
ISRO further noted that all subsystems used in the test were rigorously qualified before integration into the PHTA. The ignition sequence was derived from a series of hot tests at the single-element level. To ensure a smooth ignition process during the PHTA test, another test article, the Pre-burner Ignition Test Article (PITA), was developed. This included the pre-burner along with its feed systems, start-systems, and control components. A series of tests on the PITA helped derive the optimal start sequence for the power head test article.
Disclaimer: This image is taken from Reuters.